Cold Neutron Heated Tomography
Scope of the projet
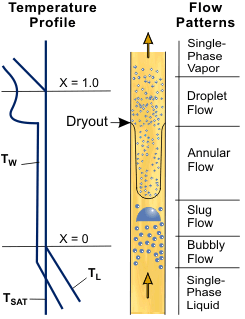
The capacity of a coolant to remove the heat generated in nuclear fuel represents one of the strongest constraints to nuclear power generation. In boiling water reactors a dryout of the coolant film on the fuel rods in the annular flow regime represents the ultimate failure in heat removal which, at typical power reactor conditions, leads to damage of the nuclear fuel. Although known since the beginning of nuclear power, the dryout phenomenon cannot be predicted by fundamental simulations based on continuum mechanics. For the purpose of reactor design and safety analyses it is described by empirical models fitted to experiments. This is due to the complexity of multiphase flows, aggravated by complicated boundary conditions. Computational fluid dynamics has made significant progress in the modelling of two-phase flows using different approaches. Large Eddy Simulation coupled with a surface tracking method for the gas-liquid interface is a potential candidate for solving the problem of dryout prediction. Functional spacer grids equipped with vanes for the flow control are used to enhance the heat transfer and to delay dryout. A future availability of computational tools to predict the performance of the highly complex flow fields in such geometries will lead to an acceleration of the further optimization of nuclear fuel elements, which is expected to yield considerable advances in efficiency, economy and safety. The planned work concerns experiments on dryout in the geometry of the cooling subchannel of a nuclear fuel element equipped with a functional spacer with the main purpose to supply data supporting the model development and applicable for the validation of the computer codes.
Research Tasks
The planned research aims at constructing a downscaled fuel test facility in order to visualize the dryout and similar flow phenomena in a heated test channel. The main quantity of interest is the liquid holdup and its spatial distribution. The identification of the location of dryout by a liquid film thickness measurement, a determination of the share of liquid flowing in the film and transported by droplets in the vapor bulk flow as well as the effect of the functional spacer grids on these characteristics requires high-resolution instrumentation. Since goal of the work does not consist in a direct qualification of fuel element designs for the application in power plants, but rather in the development and validation of codes based on fundamental fluid dynamics, the experiments can be performed in a downscaled mockup with model fluids. The main type of instrumentation will be cold neutron tomography. The ICON beam line at the Paul Scherrer Institute or an alternative beam line will be used as neutron source. As a reference method, X-ray radiography will be applied. The performance of different functional spacer designs will be analyzed and compared. The data obtained will be useful for CFD code validation in the future.
For further information contact Christian Bolesch
Contact
No database information available